Legierungen verstehen
Heutige Werkstoffe sind in der Praxis ein Gemenge verschiedener chemischer Elemente, man spricht in solchen Fällen auch von einer „Legierung“. Stahl und Gusseisen sind im Grunde genommen Legierungen auf Basis von Eisen (Fe) mit Zulegierung von Kohlenstoff (C), der für die Härte des Eisenwerkstoffes verantwortlich ist. Anhand der Mikrostruktur kann dann auf Eigenschaften der Legierung wie deren Festigkeit, Härte und Zähigkeit geschlossen werden.
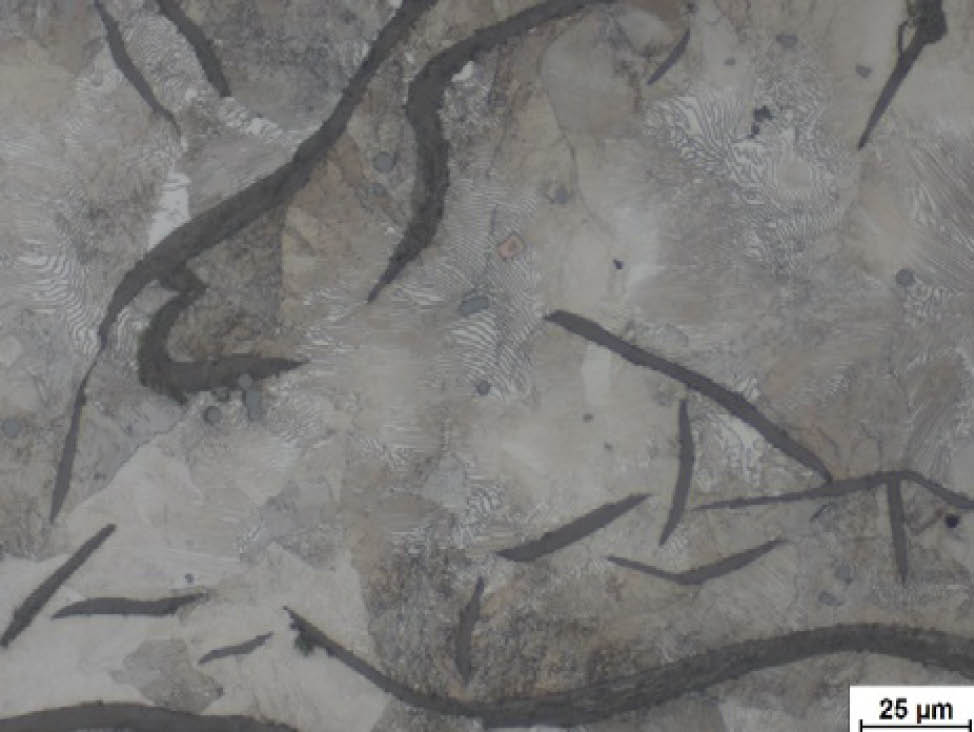
Abb. 3: Perlitisches Gusseisen mit Lamellengraphit, geätzt mit Nital. Der Kohlenstoff tritt hauptsächlich als Graphit in lamellarer Form auf, was eine verminderte Festigkeit zur Folge hat. Die perlitische Matrix selber hat eine ausreichend hohe Härte.
Bild aufgenommen mit ZEISS Axio Imager, Objektiv 50x, Hellfeld
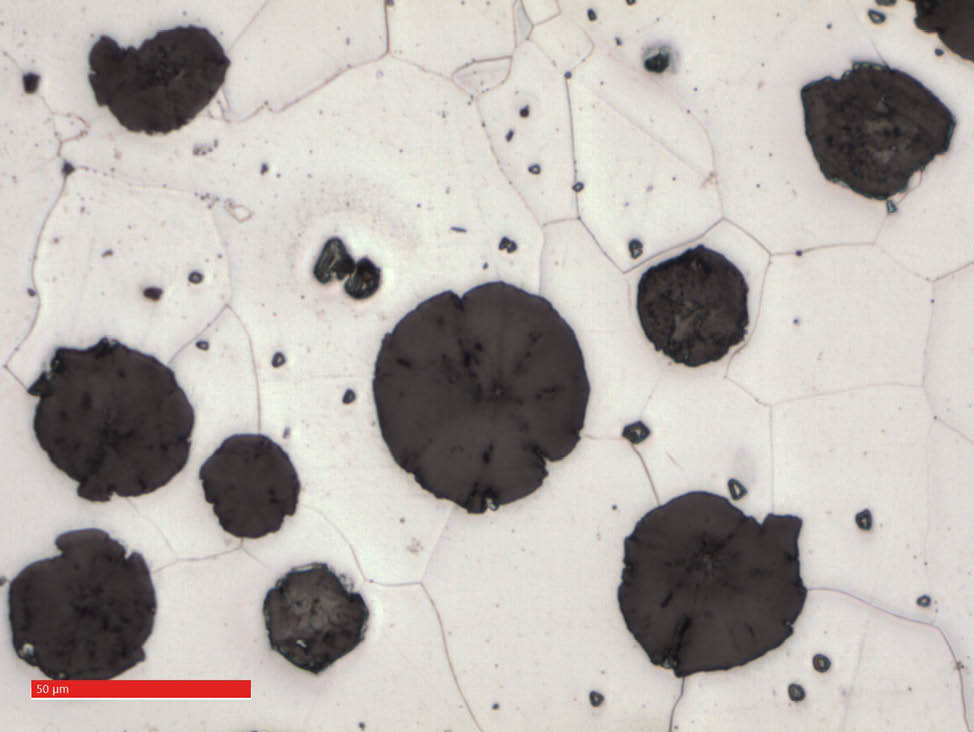
Abb. 4: Ferritisches Gusseisen mit Kugelgraphit, geätzt mit Nital. Der Kohlenstoff tritt hauptsächlich als Graphit in kugeliger Form auf. Die Kugelform bewirkt eine bessere Festigkeit im Vergleich zu lamellarem Gusseisen, die Härte des Werkstoffes ist jedoch aufgrund des fehlenden Zementits im rein ferritischen Grundgefüge geringer.
Bild aufgenommen mit ZEISS Smartzoom 5, Vergrößerung: ca. 500x
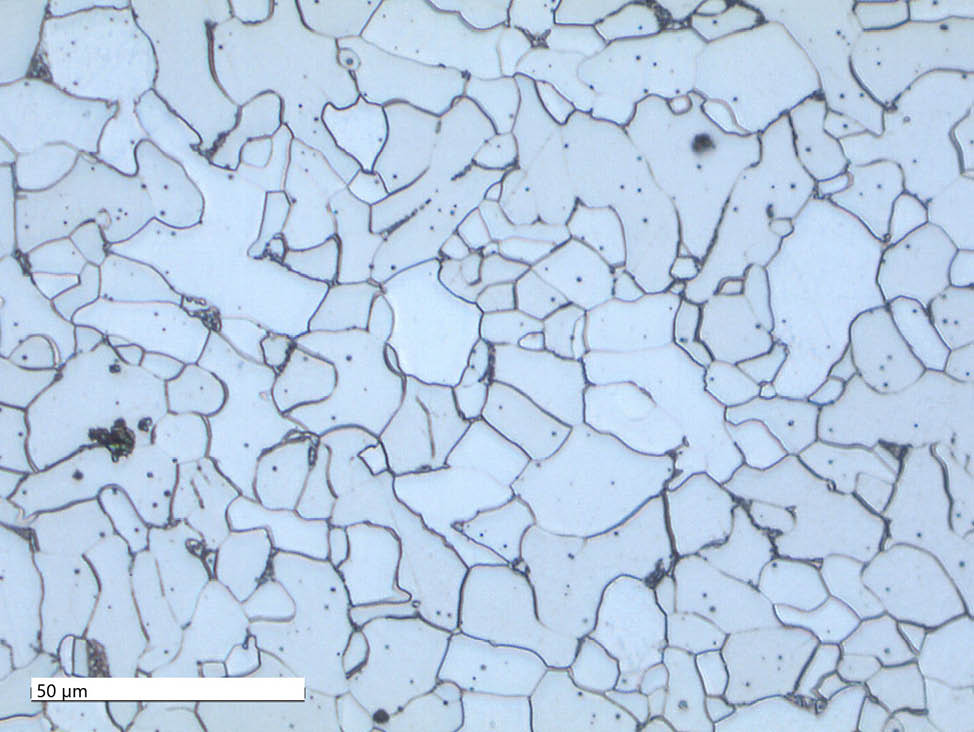
Abb. 5: Ferritischer Stahl mit ca. 0,1% C, geätzt mit Nital. Der Kohlenstoff tritt hauptsächlich als Zementit und im geringen Anteil von Perlit zwischen den Ferritkörnern auf. Das somit fast rein ferritische Gefüge hat eine geringe Härte, aber eine sehr gute Zähigkeit.
Bild aufgenommen mit ZEISS Smartzoom 5, Vergrößerung 500x, Koaxialbeleuchtung mit geringem Ringlichtanteil
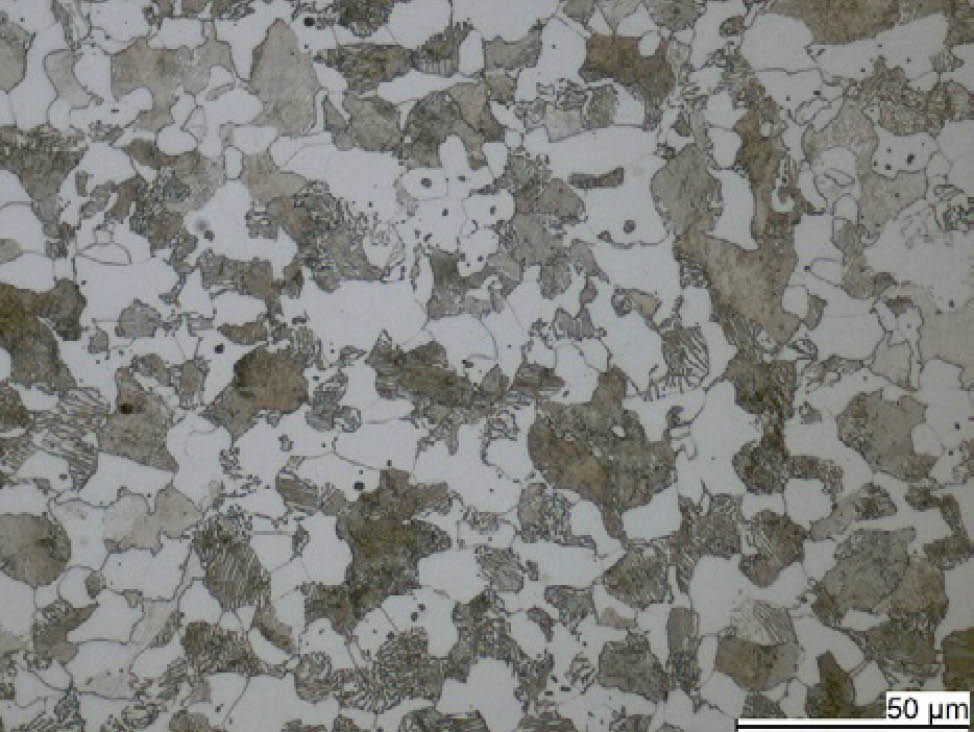
Abb. 6: Ferritisch-perlitischer Stahl mit ca. 0,2 % C, geätzt mit Nital. Der Kohlenstoff tritt hauptsächlich als Zementitlamelle im härteren perlitischen Anteil neben den Ferritkörnern auf. Dadurch erscheint der Zementit streifig. Das perlitische Korn reflektiert weniger Licht als das ferritische und erscheint deshalb dunkler. Ein solches Gefüge hat eine höhere Härte als der Stahl in Abb. 5, aber eine geringere Zähigkeit.
Bild aufgenommen mit ZEISS Axiolab, Objektiv 50x, Hellfeld