Herausforderungen bei der Präparation von mikroelektronischen Proben
Beim kontrollierten Materialabtrag und bei der Zielpräparation von mikroelektronischen Proben treten drei Herausforderungen besonders häufig auf.
Die geringen Abmessungen verlangen spezielle Geräte und entsprechendes Zubehör, die für die Handhabung sehr kleiner Proben geeignet sind. Aufgrund der Abmessungen, die normalerweise im Mikrometerbereich liegen, ist auch bei Schritten wie dem Trennen und Schleifen eine höhere Genauigkeit als üblich erforderlich.
Die Materialzusammensetzung ist komplex, da in der Regel weiche Metalle, Keramik und Verbundstoffe dicht zu mikroelektronischen Bauteilen verbaut sind. Dies verlangt Kompromisse bei der Wahl der Präparationsmethode und Parameter, die sorgfältig auf die vorgegebenen Anforderungen abgestimmt werden müssen.
Ein kontrollierter Materialabtrag und eine genaue Präparation sind unerlässlich, wenn kleine Ziele untersucht werden. Die Prüfung einer metallographischen Probe umfasst häufig die Untersuchung eines bestimmten Bereichs des Packagings verbundener Chips. Das kann sehr zeitaufwändig sein, da für den kontrollierten Materialabtrag eine Technik mit manuellem Schleifen mit anschließendem Prüfen verwendet wird, d. h. wiederholtes Schleifen und Prüfen, bis das Ziel sichtbar ist und poliert werden kann.
In der Forschung und bei der Fehleranalyse kann das Verfehlen eines Ziels beim manuellen Schleifen mit anschließendem Prüfen den Verlust einer einmaligen und teuren Probe bedeuten. Aus diesem Grund werden zunehmend automatisierte und optimierte Lösungen verwendet, die sich durch hohe mechanische Präzision, optische Messeinheiten und spezielle Probenhalter auszeichnen.
Häufig auftretende Probleme bei der Präparation von mikroelektronischen Proben:
- Trennen: Splittern oder Risse bei Silizium-Wafern, Glas oder Keramik.
- Einbetten: Mechanische Verformung und thermische Beschädigung.
- Schleifen: Brechen der spröden Bestandteile, wie Glasfasern oder Keramik
- Polieren: Verschmieren weicher Metalle; Reliefs aufgrund von Härteunterschieden der Werkstoffe einer Komponente; Siliziumkarbid und Diamantpartikel im Lot
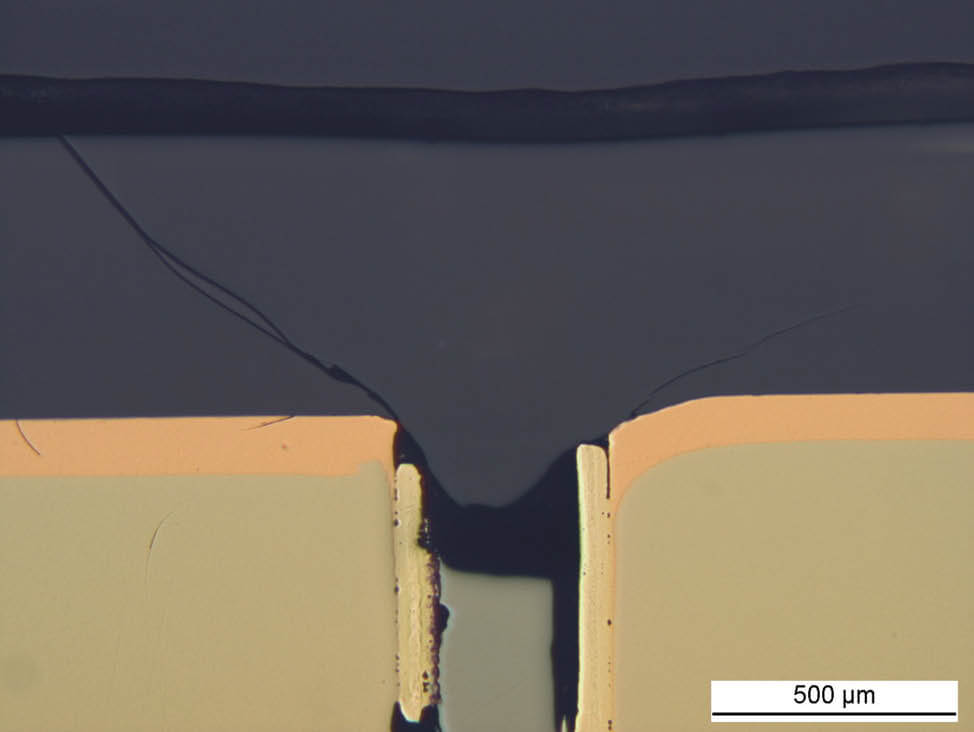
Abb. 7: Erkennung eines Risses in einer Diode
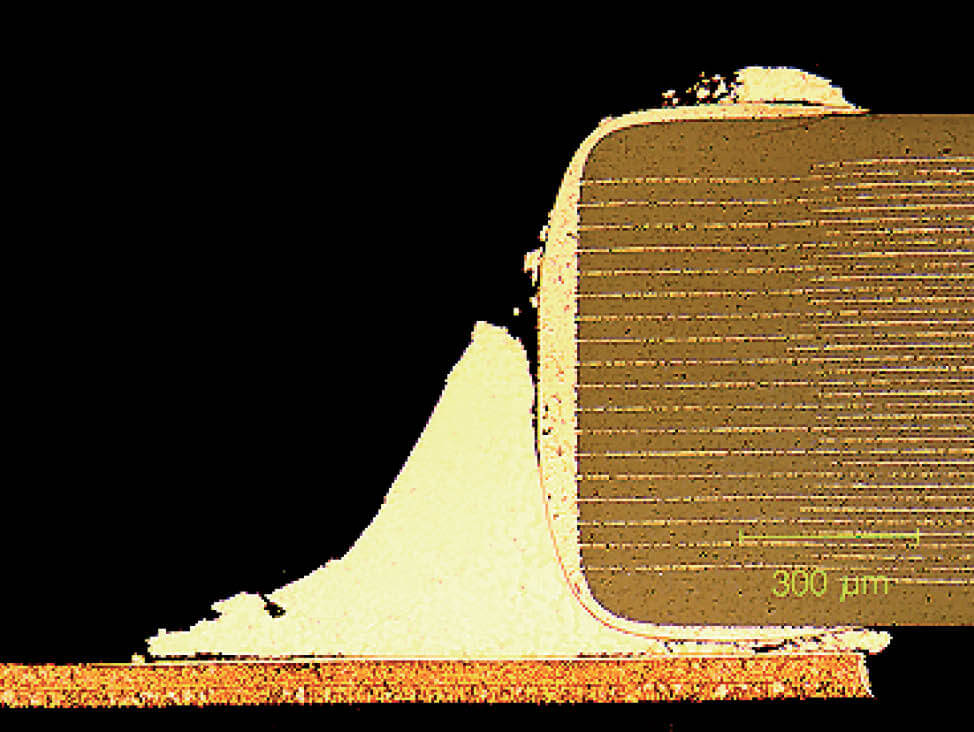
Abb. 8: Querschliff durch einen alten Mehrschicht-Keramikkondensator mit Ermüdungsrissen der Lötverbindung
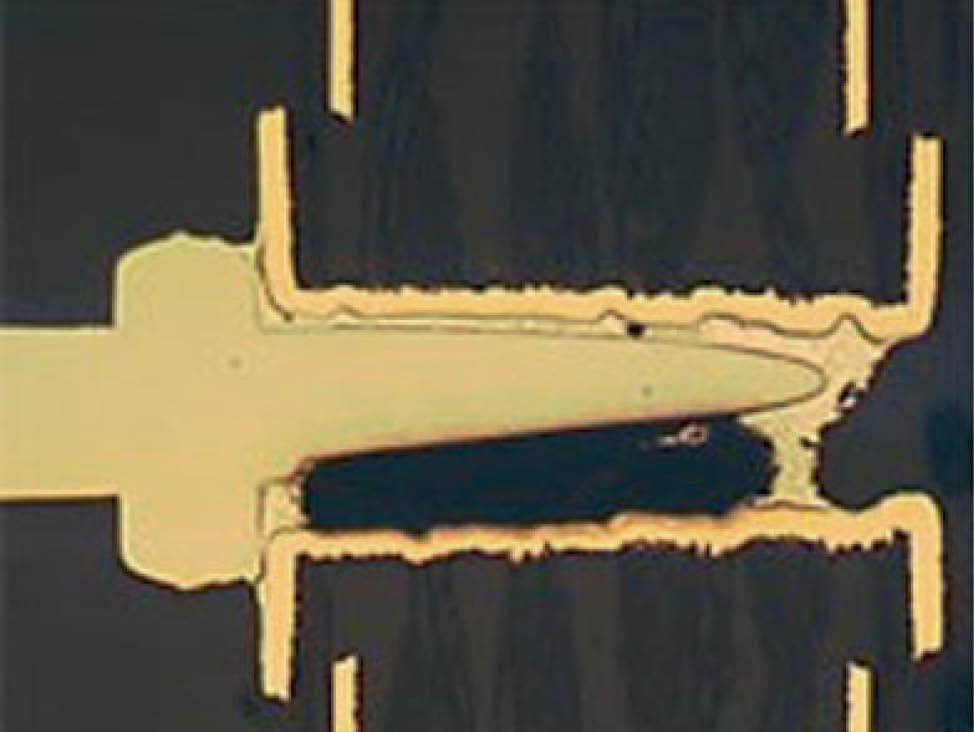
Abb. 9: Großer Hohlraum in einer Lötverbindung auf einer Leiterplatte (50x)
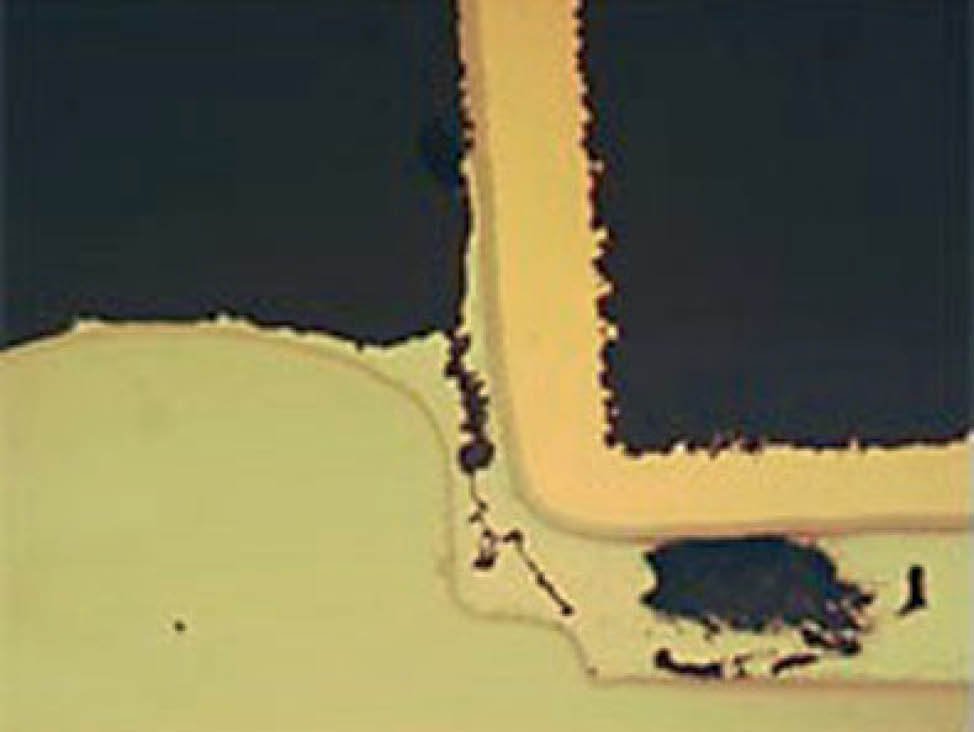
Abb. 10: Hohlraum und Riss in einer Lötverbindung auf einer Leiterplatte (200x)
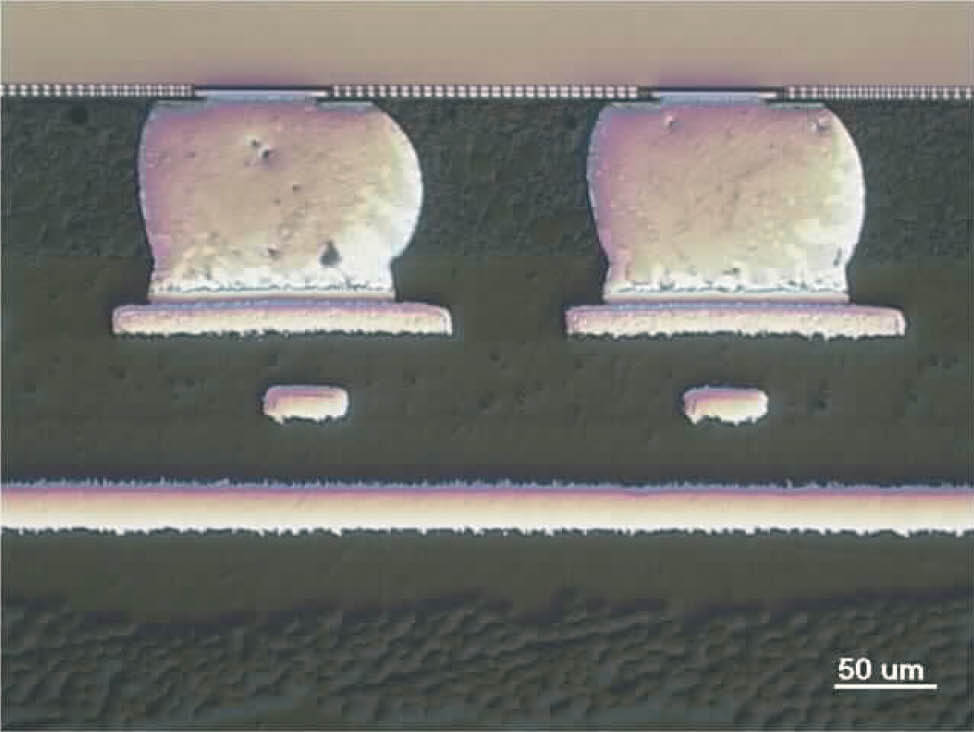
Abb. 11: Querschliff von Lotperlen, DIC