Probleme bei der Präparation von thermischen Spritzschichten
Es ist nach wie vor umstritten, wie die wahre Porosität einer metallographisch präparierten Spritzschicht zu beurteilen ist, da unsachgemäßes Schleifen und Polieren Artefakte erzeugt, die nicht Teil des Gefüges sind.
So kann bei einer Beschichtung aus Metall oder Metall/Keramik das weichere Metall beim Schleifen in die Poren gedrückt werden und dadurch bei unsachgemäßem Polieren die wahre Porosität verschleiern. Keramikbeschichtungen wiederum sind so spröde, dass Partikel beim Schleifen aus der Oberfläche brechen können. Ohne sorgfältiges Polieren können Ausbrüche den Eindruck hoher Porosität vortäuschen.
Häufig auftretende Probleme bei der Vorbereitung thermischer Spritzschichten für die metallographische Analyse:
Trennen: Beim Einspannen von spritzbeschichteten Werkstücken können Risse in spröden Beschichtungen entstehen oder sehr weiche Beschichtungen können komprimiert werden.
Einbetten: Kalteinbettmittel mit hoher Schrumpfung können Schichten mit geringer Haftung vom Grundmaterial ablösen. Schrumpfspalte können auch zur Ablösung der Schicht führen, wenn diese während des Schleifens und Polierens nicht durch das Einbettmittel gestützt wird.
Schleifen und Polieren: Kantenabrundung kann zu einer ungleichmäßigen Politur führen, woraus sich eine falsche Interpretation der Porosität ergeben kann. Außerdem kann Relief zwischen Beschichtung und Substrat einen Schatten verursachen, der zu falschen Interpretationen führen kann.

Abb. 1: Keramikspritzschicht, unzureichend poliert
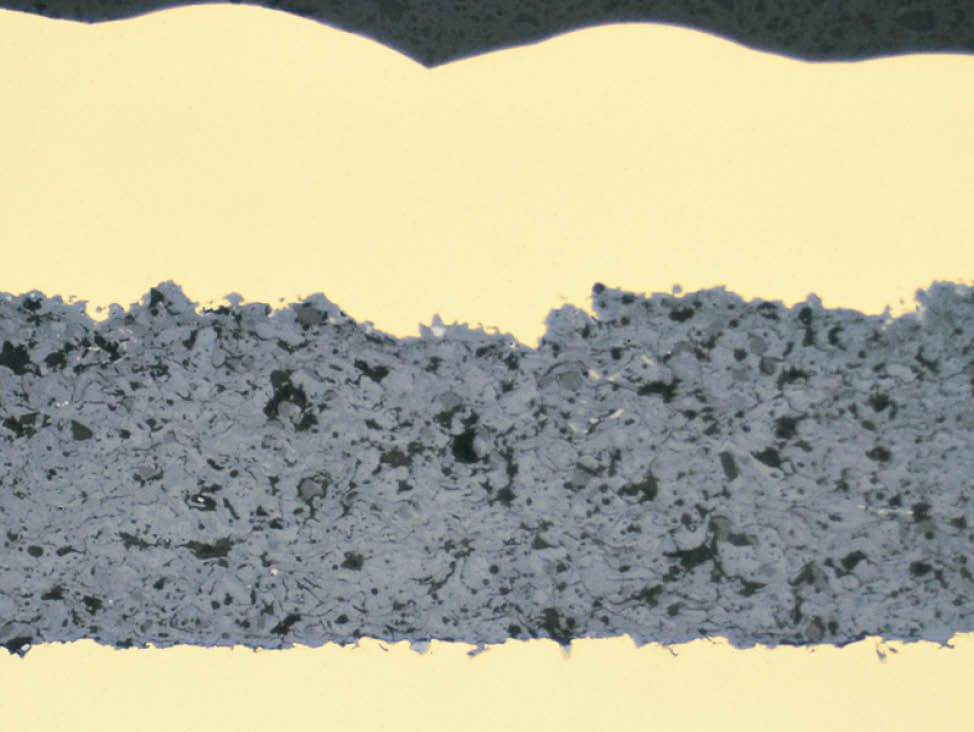
Abb. 2: Selbe Beschichtung wie Abb. 1, korrekt poliert

Abb. 3: Kantenabrundung kann zu ungleichmäßigem Polieren führen, woraus sich eine falsche Interpretation der Porosität ergeben kann. In diesem Fall täuscht ungenügendes Polieren weniger Porosität in der Mitte der Schicht vor
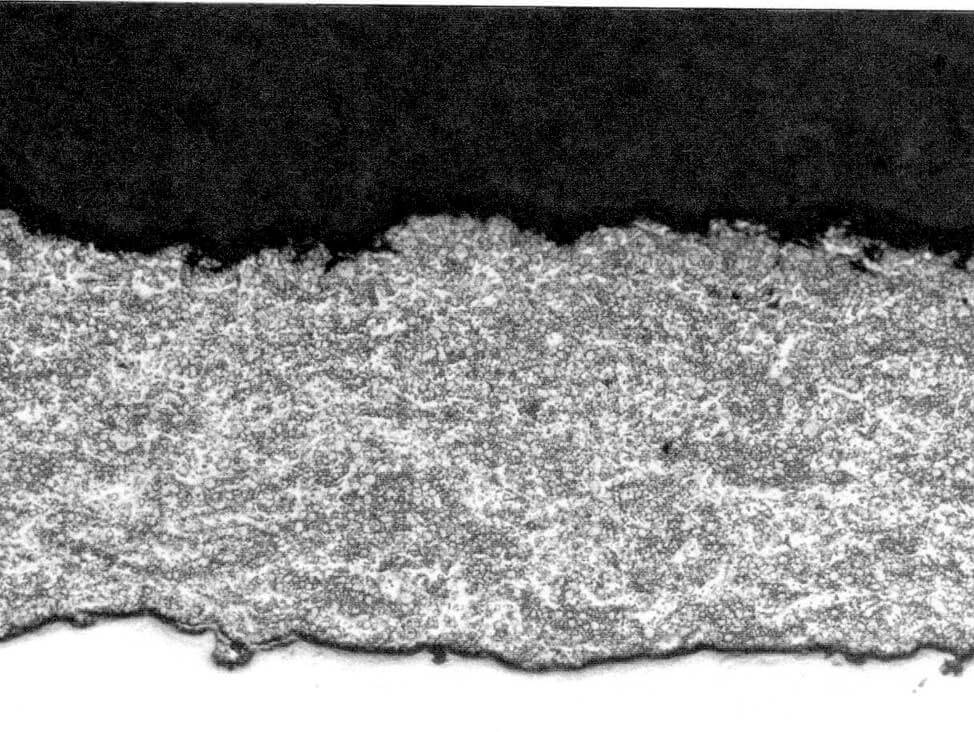
Abb. 4: Relief zwischen Beschichtung und Substrat verursacht einen Schatten, der zu falschen Interpretationen führen kann. In diesem Fall zeigt eine WC/Co-Spritzschicht mit Polierrelief eine dunkle Linie an der Grenzfläche Einbettmittel/Spritzschicht