Conoscere le leghe
I materiali utilizzati oggi nelle applicazioni pratiche sono una miscela di diversi elementi chimici, spesso indicati come "leghe". L'acciaio e la ghisa, ad esempio, sono essenzialmente leghe a base di aggiunte di ferro (Fe) e carbonio (C), che determinano la durezza del materiale ferroso. L'analisi microstrutturale ci permette di trarre conclusioni sulle proprietà della lega, tra cui la resistenza, durezza e duttilità
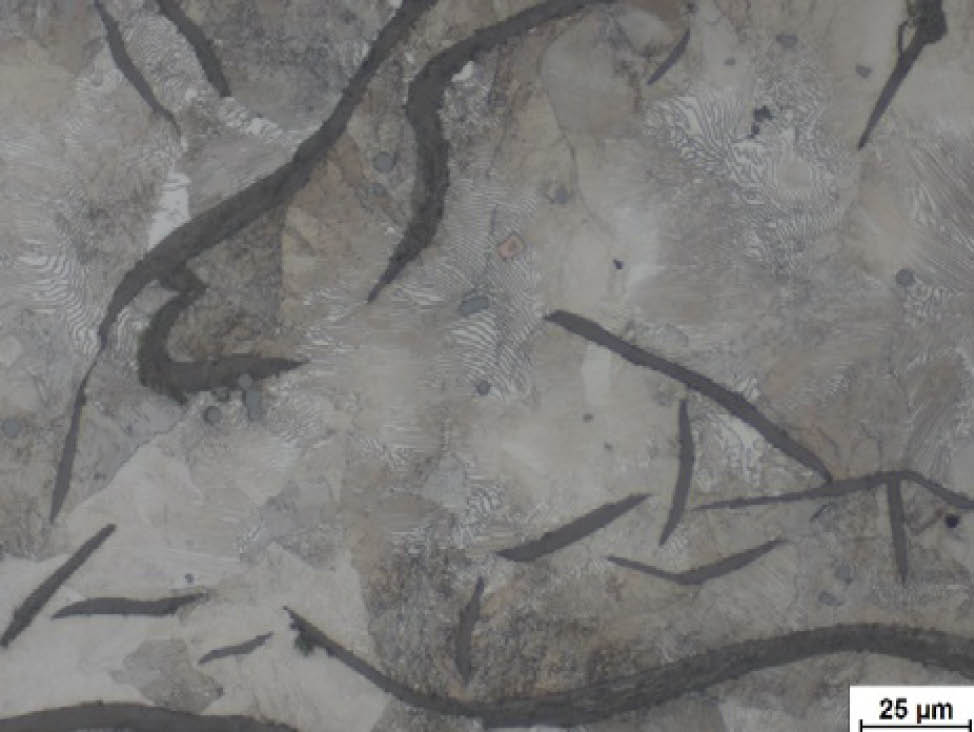
Fig. 3: Ghisa perlitica a grafite lamellare, attaccata con Nital. Il carbonio è presente principalmente come grafite in forma lamellare, con conseguente riduzione della resistenza. La matrice perlitica stessa ha un grado di durezza sufficientemente elevato.
Immagine scattata con ZEISS Axio Imager, obiettivo 50x, illuminazione in campo chiaro
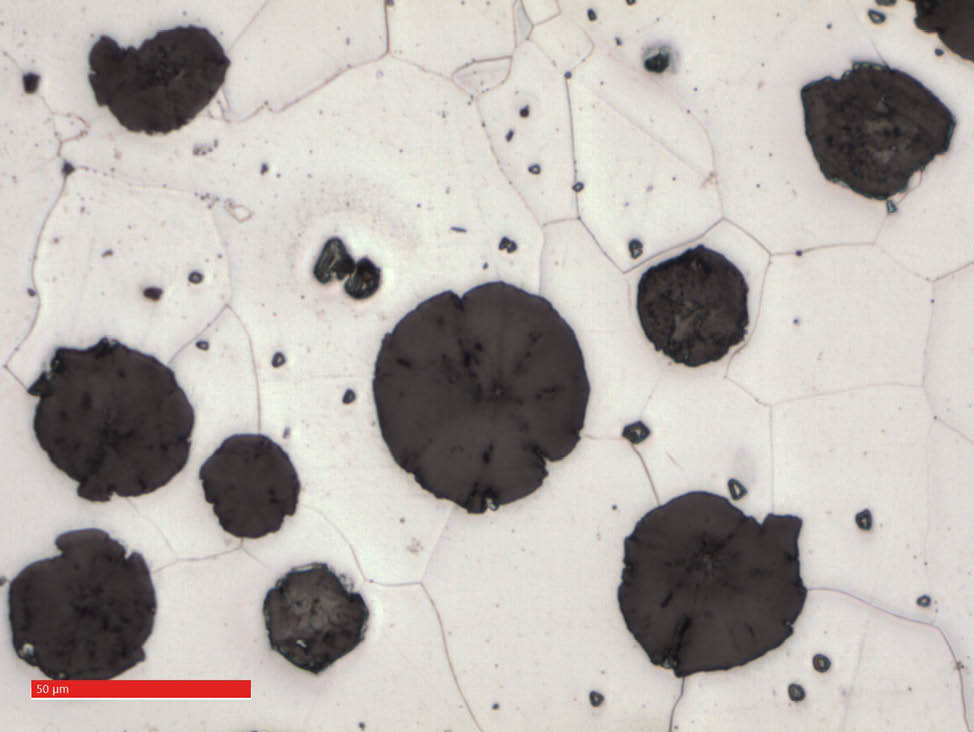
Fig. 4: Ghisa ferritica con grafite sferoidale, attaccata con Nital. Il carbonio è presente principalmente come grafite in forma sferica. La forma sferica conferisce maggiore robustezza rispetto alla ghisa lamellare, ma la durezza del materiale è inferiore a causa dell'assenza di cementite nella matrice puramente ferritica.
Immagine scattata con ZEISS Smartzoom 5, ingrandimento di circa 500x
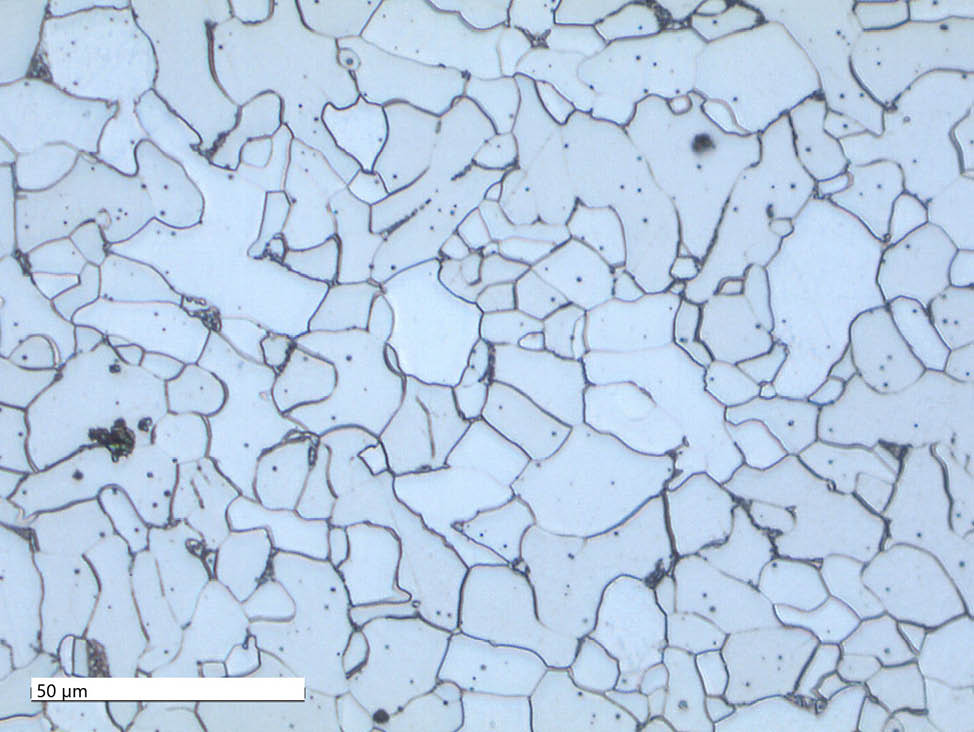
Fig. 5: Acciaio ferritico con circa lo 0,1% di C, attaccato con Nital. Il carbonio è presente principalmente sotto forma di cementite con una piccola percentuale di perlite tra i grani ferritici. La matrice quasi puramente ferritica, presenta un basso grado di durezza ma ottima duttilità.
Immagine scattata con ZEISS Smartzoom 5, ingrandimento di circa 500x, illuminazione coassiale con bassa proporzione di luce anulare
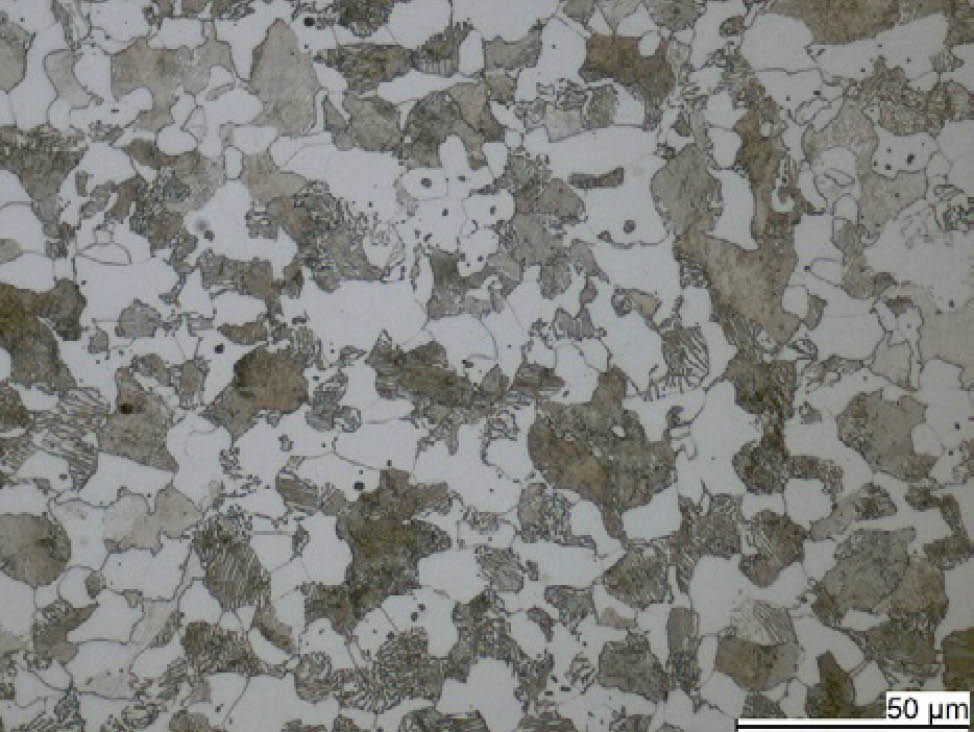
Fig. 6: Acciaio ferritico-perlitico con circa lo 0,2% di C, attaccato con Nital. Il carbonio è presente principalmente come cementite lamellare e in percentuale maggiore di perlite adiacente ai grani ferritici. Ciò conferisce alla cementite un aspetto striato. I grani perlitici riflettono meno luce dei grani ferritici e quindi appaiono più scuri. Una matrice di questo tipo ha una maggiore durezza, ma una scarsa duttilità.
Immagine scattata con ZEISS Axiolab, obiettivo 50x, illuminazione in campo chiaro